Guide Lean Manufacturing : Optimisez vos flux logistiques et réduisez les gaspillages
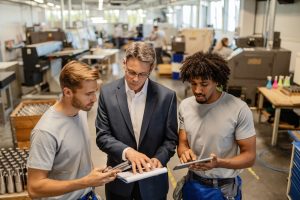
Introduction au lean manufacturing
Le lean manufacturing, souvent simplement appelé „lean“, est une approche systématique visant à éliminer les gaspillages dans le processus de production, tout en améliorant la qualité et l’efficacité. Ce concept, largement adopté dans le secteur industriel, est devenu un incontournable pour les entreprises cherchant à optimiser leurs flux logistiques, réduire les coûts et améliorer la satisfaction client.
L’origine du lean manufacturing remonte aux pratiques de production de Toyota dans les années 1930. Aujourd’hui, ces principes sont appliqués dans de nombreux secteurs, de l’automobile à l’aérospatiale, en passant par l’agroalimentaire.
Les principes fondamentaux du lean manufacturing
Pour les débutants, il est crucial de comprendre les bases du lean manufacturing avant de l’appliquer dans un contexte réel. Voici les cinq principes fondamentaux :
- Identifier la valeur : Comprendre ce que le client considère comme valeur est la première étape. Il s’agit de tout ce pour quoi le client est prêt à payer.
- Cartographier la chaîne de valeur : Une fois la valeur définie, il est essentiel de cartographier toutes les étapes du processus de production. Cette cartographie permet d’identifier les étapes qui ajoutent de la valeur et celles qui n’en ajoutent pas.
- Créer un flux continu : L’objectif ici est d’organiser les processus de manière à ce que les produits se déplacent sans interruption d’une étape à l’autre.
- Établir un système de production en flux tiré : Ce principe consiste à produire uniquement ce qui est nécessaire, quand c’est nécessaire. Cela permet de réduire les stocks inutiles et d’améliorer l’efficacité.
- Poursuivre la perfection : Le lean est un processus d’amélioration continue. Chaque amélioration conduit à une nouvelle opportunité d’amélioration, créant ainsi un cycle de perfectionnement sans fin.
L’importance de l’optimisation des flux logistiques
Dans le cadre du lean manufacturing, l‘optimisation des flux logistiques internes joue un rôle central. Les flux logistiques englobent toutes les activités liées au transport, à la gestion des stocks, et à la distribution des matériaux au sein de l’entreprise. En optimisant ces flux, une entreprise peut non seulement réduire les coûts, mais aussi améliorer l’efficacité opérationnelle et la qualité du service.
Le concept de train logistique, ou „milkrun“, est un excellent exemple de cette optimisation. Il s’agit de systèmes de transport internes conçus pour améliorer l’approvisionnement en bord de ligne en supprimant les déplacements inutiles, ce qui permet d’optimiser les ressources et de sécuriser les flux.
Les outils essentiels du lean manufacturing
Pour bien démarrer avec le lean manufacturing, il est essentiel de comprendre les outils qui permettent d’implémenter cette méthode de manière efficace. Voici quelques-uns des outils les plus couramment utilisés :
- 5S : Un outil de gestion visuelle qui aide à organiser un lieu de travail pour qu’il soit plus efficace et moins encombré. Les cinq „S“ sont Seiri (trier), Seiton (ranger), Seiso (nettoyer), Seiketsu (standardiser), et Shitsuke (maintenir la discipline).
- Kaizen : Ce concept japonais signifie „amélioration continue“. Il s’agit d’encourager tous les employés, à tous les niveaux, à rechercher constamment des moyens d’améliorer les processus de travail.
- Kanban : Un système de gestion des flux qui utilise des cartes visuelles pour signaler la nécessité de réapprovisionner ou de produire plus de matériaux. Le Kanban est souvent utilisé pour gérer les stocks et la production en temps réel, ce qui permet de maintenir un flux constant et sans interruption.
- Valeur ajoutée et non-valeur ajoutée : Ce concept consiste à identifier et éliminer toutes les activités qui n’ajoutent pas de valeur au produit final. Cela peut inclure des étapes de production inutiles, des déplacements non essentiels, ou des stocks excédentaires.
- Le train logistique : Comme mentionné précédemment, le train logistique est un excellent outil pour optimiser les flux internes en réduisant les trajets non nécessaires et en améliorant l’efficacité du transport de matériaux au sein de l’usine.
Pourquoi adopter le lean manufacturing ?
L’adoption du lean manufacturing présente plusieurs avantages pour les entreprises, en particulier dans des secteurs compétitifs où l’efficacité et la réactivité sont primordiales. Voici quelques raisons pour lesquelles votre entreprise devrait envisager de passer au lean :
- Réduction des coûts : En éliminant les gaspillages, le lean manufacturing permet de réduire les coûts de production. Moins de ressources sont nécessaires pour produire les mêmes résultats, ce qui améliore la marge bénéficiaire.
- Amélioration de la qualité : Le focus sur l’amélioration continue et la réduction des erreurs conduit à une qualité supérieure des produits finis. Cela se traduit par une plus grande satisfaction des clients et une réduction des retours ou des réclamations.
- Flexibilité accrue : Le lean manufacturing permet à une entreprise de s’adapter plus rapidement aux changements du marché. Les processus de production plus flexibles et plus réactifs permettent de répondre plus efficacement à la demande des clients.
- Engagement des employés : En impliquant tous les niveaux de l’organisation dans l’amélioration continue, le lean manufacturing favorise un meilleur engagement des employés. Cela conduit à une culture d’entreprise plus forte et à un environnement de travail plus motivant.
- Optimisation des flux logistiques : L’amélioration des flux logistiques internes est un élément clé du lean. En optimisant le transport des matériaux et en réduisant les temps de déplacement, les entreprises peuvent augmenter leur productivité tout en réduisant les délais de production.
Cas d’utilisation : L’importance du train logistique
Un excellent exemple de la mise en œuvre réussie du lean manufacturing est l’utilisation du train logistique dans les grandes entreprises industrielles. Le train logistique est non seulement un outil d’optimisation des flux, mais il contribue également à améliorer la sécurité au sein de l’usine en réduisant le besoin d’utilisation de chariots élévateurs et autres équipements de manutention potentiellement dangereux.
De plus, l’intégration de systèmes comme le train logistique permet de maximiser l’espace de production en éliminant les allées encombrées. Ainsi, non seulement l’efficacité est améliorée, mais la sécurité des travailleurs est également renforcée.
L’impact du lean manufacturing sur la chaîne d’approvisionnement
Le lean manufacturing ne se limite pas à l’optimisation des processus internes d’une entreprise ; il a également un impact significatif sur la chaîne d’approvisionnement globale. En appliquant les principes du lean à l’ensemble de la chaîne, les entreprises peuvent atteindre un niveau de synchronisation et d’efficacité sans précédent.
Réduction des stocks et juste-à-temps
L’un des aspects les plus puissants du lean manufacturing est la réduction des stocks grâce à la mise en place du système de production en flux tiré, souvent associé au concept de „juste-à-temps“ (JAT). Plutôt que de produire en masse et de stocker des quantités importantes de produits finis ou de matières premières, le lean encourage la production en fonction de la demande réelle. Cela signifie que les matériaux sont approvisionnés et transformés exactement au moment où ils sont nécessaires, ce qui réduit considérablement les coûts de stockage et les risques de surproduction.
L’optimisation des flux logistiques internes joue un rôle crucial dans cette approche, en assurant que chaque pièce arrive au bon moment et au bon endroit dans le processus de production.
Collaboration renforcée avec les fournisseurs
Le lean manufacturing encourage également une collaboration plus étroite avec les fournisseurs. En partageant des informations en temps réel sur les besoins de production et les prévisions de demande, les entreprises peuvent aligner leurs opérations avec celles de leurs fournisseurs. Cela permet non seulement de réduire les délais de livraison, mais aussi d’améliorer la qualité des matériaux entrants, réduisant ainsi les risques de défauts et de non-conformité.
De plus, les relations à long terme avec les fournisseurs, basées sur la confiance et la transparence, favorisent l’innovation conjointe et l’amélioration continue des processus.
Comment adopter le lean manufacturing dans votre entreprise
Adopter le lean manufacturing peut sembler complexe, surtout pour les entreprises qui en sont à leurs débuts. Voici quelques étapes pour vous aider à démarrer :
- Former vos équipes : Le succès du lean manufacturing repose en grande partie sur l’engagement des employés à tous les niveaux. Assurez-vous que vos équipes comprennent les principes du lean et sont formées à l’utilisation des outils tels que le 5S, le Kaizen, et le Kanban.
- Commencer par un projet pilote : Plutôt que de transformer toute l’entreprise d’un coup, commencez par un projet pilote dans une section spécifique de votre production. Cela vous permettra de tester les concepts du lean et de prouver leur valeur avant de les déployer à plus grande échelle.
- Cartographier vos processus actuels : Utilisez des techniques comme la cartographie de la chaîne de valeur pour identifier les points faibles dans vos processus actuels. Cela vous aidera à cibler les zones où le lean manufacturing peut avoir l’impact le plus immédiat.
- Implémenter des outils de suivi : Pour évaluer l’efficacité de vos initiatives lean, il est crucial de mettre en place des outils de suivi de performance. Cela pourrait inclure des indicateurs de performance clés (KPI) pour mesurer la réduction des gaspillages, l’amélioration de la qualité, et la satisfaction des clients.
- S’engager dans l’amélioration continue : Le lean manufacturing n’est pas une destination, mais un voyage. Engagez-vous à poursuivre l’amélioration continue en sollicitant régulièrement des retours d’information de la part de vos employés et en analysant les performances de manière proactive.
In fine, le lean manufacturing est une méthode éprouvée pour améliorer l’efficacité, réduire les coûts, et augmenter la satisfaction des clients. En adoptant ces principes dans votre entreprise, vous pouvez transformer vos opérations et vous positionner pour un succès durable dans un environnement économique de plus en plus compétitif.
L’optimisation des flux logistiques internes grâce à des solutions comme le train logistique est une composante essentielle de cette transformation. En réduisant les gaspillages et en améliorant la qualité, le lean manufacturing peut non seulement améliorer la performance de votre entreprise, mais aussi renforcer la sécurité et l’engagement de vos employés.
Si vous envisagez d’adopter le lean manufacturing, commencez dès aujourd’hui en formant vos équipes, en cartographiant vos processus, et en mettant en œuvre des projets pilotes. La route vers l’efficacité et l’amélioration continue commence ici.
Faites confiance à ManuLine pour l’optimisation des flux logistiques internes
Manuline offre des solutions intralogistiques novatrices parfaitement adaptées aux exigences particulières des entreprises. Nos modèles de train logistique sont conçus pour offrir une flexibilité, une modularité et une conformité optimales avec les principes du Lean Manufacturing.
Explorez notre gamme complète de solutions sur mesure pour le transport de charges internes ci-dessous :
CONTACTEZ-NOUS